Stretch film is a versatile packaging material widely used in industries for securing and protecting pallets and products during storage and transportation. Proper application of stretch film is crucial to ensure stability and safeguard the integrity of goods. In this article, we will explore the best practices for applying stretch film, covering key considerations to achieve optimal results and maximize efficiency.
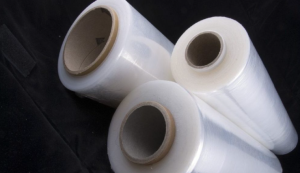
1. Selecting the Right Stretch Film:
Before delving into application techniques, it is essential to choose the appropriate stretch film for the specific application. Factors to consider include film thickness, load weight, load stability requirements, and environmental conditions. Opt for high-quality stretch film that offers excellent puncture resistance, elongation, and cling attributes to ensure optimal performance.
2. Preparing the Pallet:
Ensure the pallet is clean, dry, and in good condition before applying stretch film. Remove any debris, protruding nails, or damaged boards that can hinder proper wrapping or compromise load stability. Additionally, arrange the products on the pallet in a stable and uniform manner to facilitate even distribution of the film.
3. Establishing Proper Tension:
Achieving the right tension during stretch film application is crucial to secure the load effectively without causing damage. Too little tension can result in loose film and inadequate load stability, while excessive tension can cause product damage or excessive film elongation. Aim for a balance that provides sufficient tightness while allowing for minimal film elongation.
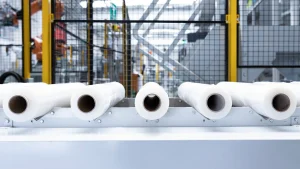
4. Applying Multiple Film Layers:
For optimal load stability, consider applying multiple layers of stretch film. This technique is referred to as “double wrapping” or “crossover wrapping.” Start by applying a lower layer of film, wrapping it around the pallet and products in a consistent manner. Then, apply a second layer in the opposite direction (perpendicular to the first layer) to create a secure and robust wrapping structure.
5. Overlapping Film Layers:
Ensure proper overlap between film layers during application to enhance load stability. The recommended overlap is typically between 50% to 70% of the film width. This overlap facilitates an interlocking effect, creating a stronger bond between adjacent film layers and minimizing the risk of film unraveling or loosening during transportation or storage.
6. Securing the Film Ends:
Properly secure the film ends to prevent unraveling and maintain load integrity. Consider using accessories like stretch film hooks or mechanical film brake devices to anchor the film ends securely. Alternatively, hand tying or using specialized adhesive tapes can also be effective methods for immobilizing the film ends.
7. Maintaining Consistent Film Tension:
To ensure even load containment, maintain consistent tension throughout the entire application process. Avoid abrupt changes in tension, such as sudden release or excessive pull, as this can lead to load shifting or film breakage. Consistency in tension promotes load stability and minimizes the risk of damages during transit or storage.
Proper application of stretch film is vital for ensuring the safe transportation and storage of pallets and products. By following these best practices, including selecting the right stretch film, establishing proper tension, utilizing multiple film layers, overlapping film layers, securing film ends, and maintaining consistent tension, companies can enhance load stability, minimize damages, and optimize packaging efficiency. Implementing these techniques fosters a reliable and secure packaging solution that safeguards goods throughout their journey in the supply chain.